i - BOSS Manufacturing
is an Enterprise Resource Planning (ERP) product which helps Process Manufacturers manage their business more efficiently and profitably,
Supports multi-division / profit centers, multi-department / cost-centers. It is optimally suited for Process,
Discrete as well as Mixed Manufacturing Industries. It's flexible design and extensive parameterization allows
it to cater to changing business requirements. Its high scalability ensures that the usage of the application
grows with the growth of the business.
Salient features:
- Oracle based i - BOSS is best solution for SMEs Implemented to large enterprises also.
- Multi user operation through a centralized server
- Seamless integration across all modules
- Data captured at source, single version of truth
- On-line, menu driven user-friendly interface
- Comprehensive user definable security features
- Data Security through user level access privilege rights
- Email and SMS interface
- Auto Alert feature improves the decision making by making available the crucial information on time.
- Workflow Concepts to Fix the Authority and Responsibility of each and Every user in the value chain.
- Quality Control Module ensures the right quality of material in inward/outward, having feature of auto deduction / Bonus based on the Quality Test
- Drill down feature from Balance Sheet to Voucher, Stock Statement to Gate Entry in Forms & Reports
- Online Allocation of Stock, based on FIFO & as well as at actual during consumption.
- Direct weight Capturing from Weigh Bridge, ensuring the correct quantity - Inward & Outward
- Full functionality of Excise, Service Tax , VAT & TDS
- Attachment facility of Vital Document / Picture in Indent / Purchase Order / Item Master etc.
- Identification of Replaceable Item before fresh Issue and control throughout.
- Flexible document Numbering system on daily /monthly / yearly basis.
- Multi Unit / Multi Currency
- Inward and outward freight management with freight advice, freight rates picked up from freight master, shortage / deductions from the freight amount, duplicate payment control.
- Web Based easy to use User interface. Ready to use with variety of Explorers.
- Division wise Generation of Profit & Loss.
- Balance Sheet as per Schedule VI of Companies Act with Drill down Features and Annexure.
- Cash & Fund Flows
- Cost Sheet
Production
Stores & Spares
Marginal
i - BOSS Manufacturing Comprises of following Modules
Module Wise Scope & Functions
1. Finance & Accounts
|
- Flexible Chart of Accounts with N level of grouping
- Accounts Payable
- Accounts Receivable
- Banking
- Bank Interest
- Bank Reconciliation
- Bill Tracking & Allocations of Bills
- Accounts Day Book
- Balance Sheet
- Schedules to Balance Sheet
- Profit & Loss
- Trial Balance
- Cash Flow, Fund Flow
- Cost Sheet
Sub Module for Taxation
- VAT/ CST
- Excise, Service Tax
- TDS/ FBT
- Entry Tax
- Tax Forms Tracking & Reminder like C-forms, Waybills, and Transit Pass etc.
|
|
2. Security Gate Management
|
- Powerful system for In & Out of Material, Employee, Visitor, Vehicle.
- Any Transaction is being permitted against a valid control documents based on the document type.
- Inward Register for all vehicles
- Outward Register
- Generation of Loading & Unloading Slips
- Report of Pending Vehicle in Premises
|
|
3. Weighbridge Automation
|
- Supports inward, outward & Shifting weighment
- Item wise weighment option to capture the item wise weight if multiple items exist in a consignment.
- Accepted weight is automatically updated based on the parameter configured by Administrator / Control document like Purchase Order, Sale Order etc.
- Powerful query engine to query anything related
|
|
4. Fix Assets |
- Complete functionality of Assets Opening, Addition, Transfer, Sale and Discard
- Multiple groups can be defined in the Fixed Assets Module. Depreciation to be calculated separately, as per the Income Tax and Companies Act.
- All details of fixed assets are recorded at the time of creating individual assets. These include details like quantity of fixed assets (for instance, number of chairs, tables etc.), original cost of asset, expenses incurred for capitalization, supplier related information and others.
- All Assets are uniquely identified by the unique serialization scheme at the time of creating individual assets.
- It is geared to take care of depreciation by the Straight Line Method as well as the Written down Value Method.
- Creating the opening stock of fixed assets from the existing fixed asset register giving the initial gross block and the subsequent written down value.
- The fixed asset register can be generated in prescribed format for a financial year completely eliminating the need for a separate manual fixed asset register.
- At any time location wise assets position can be known by the users
|
|
5. Project Management |
|
|
6. Material Management
Material Management Module has following sub modules for Managing Capital / Project, Consumables and Raw Materials. |
- Purchase Management
- Inventory Management
- Receipt Management
- Rejection and Return Management
- Issue Management
- Repairing and Job Management
- Gate Pass Management
- Rack Management
a. Purchase Management
- Vendor Registration
- Capturing materials requirement through Pending Material Requisition [ Indents ]
- Determining source of supply by selecting vendors
- Generation of Enquiry or Requests for Quotations (RFQ)
- Generation of Comparative Statement [ Quotation comparison ]
- Creating and processing purchase orders with facility of amendment, cancellation & Reminders
- Linking of Quality parameters, bonus and deduction criteria with Order
- Monitoring purchase orders
b. Inventory Control.
Receipt Management
Issue Management
Rejection and Return Management
- Preparation of Material Return Note. ( Against Rejected Item )
- Preparation of Dispatch Advice ( Against Rejected Item )
- Preparation of Re-inspection note to take any material from Rejected Item to Accepted
C. Repairing and Job Management
- Generation and Tracking of Job Order to Contractors / Transporters / Service Provider.
- Generation and Tracking of Repairing Item Stores In Note
- Generation and Tracking of Repairing Gate Pass
- Generation and Tracking of GRN's for Repaired Item
- Preparation of Repairing Issue Note based on the requisition made by the department.
- Entry of Executed Jobs.
d. Gate Pass Management
Generation & Tracking of Gate passes for Non-returnable, returnable.
|
|
7. Quality Control |
Purchase / In Material
In-Process QC
- Heat No / Tapping No wise capturing of the QC data for a shift/day.
Sale / Out Material
- Facility to take quality samples and Test against Dispatch Advice / Outward Rake No, to ensure that the right quality of material can be Loaded and Dispatch.
- Auto Deduction / Bonus Rate computation at the time of billing for Prorate basis Orders on Sale Bill Generation.
|
|
8. Freight Management |
|
|
9. Production Management |
|
|
10. Sales & Distribution |
- Sales Enquiry
- Sales Quotation
- Sales Order
- Dispatch Advice
- Revision of Sales Order to Amend, Cancel or Short close the Order
- Excise & Non-excise Sales/ Excise and commercial Invoicing
- Depot Transfer and Consignment sales
- Sales Broker / Agent Management
- Captive Consumption Challan
- Excise Gate Pass / Commercial Challan linked with Weighment Slip, Freight Order,
- Q.C. Reports and test certificates
- Manufacturing Excise reports along with PLA ,RG1, RG23 A Part I & Part II, RG23 C Part II with detail Annexure
- Input Register (Form IV) along with Annexure and monthly Abstract
- ER1 (RT12) returns.
|
|
11. HR & Payroll module |
- Employee Data with qualification, Experience, Salary. Loan Details
- Mobile Issue and Bills Controlling Employee Wise
- Auto Attendance Capturing from Punch devices
- Muster Roll with OT, C-off
- Shift Management/ Leave Mgmt./ Loan Mgmt
- Appraisals.
- Payroll Generation with Auto Arrears
- Statutory Forms of PF/ ESCI/ Professional Tax/ Wage Register etc.
- Gratuity Calculation
- Income Tax Computation with Form-16 generation
- Full & Finalization of Employee
|
|
12. Plant Maintenance |
- Formation of Equipment in relation with Fix Assets
- Option to Breakdown assembly and sub assembly from an equipment
- Checklist Planning Equipment / Assembly, sub-assembly wise for Preventive Maintenance
- Option to Plan / Predict a future maintenance plan,
- Requisition of Spares required against a maintenance Plan.
- Entry of job done during shutdown / Breakdown
- Equipment History Card
|
|
13. Administration / DBA |
- Document Numbering Setting
- User Creation
- Assigning Rights and Privileges to every user for entry and reports
- Financial year creation
- Data Freezing
- Configuration of Parameters that affect the entire working of the software
- Defining of Workflow
|
|
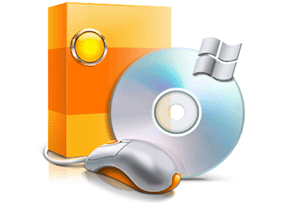
Why Choose i - BOSS ERP
- A Proven Solution with success rate of more than 90 %
- Easy Implementation, Principle Software provider does the implementation
- Highly customizable product
- Web enabled for multiple location operations
- High levels of Data Security
- Industry Expertise
- Rapid Return on Investment
- Great Price / performance ratio
- Runs on Oracle Database and Internet Developer Suite 10g
Our Products
|